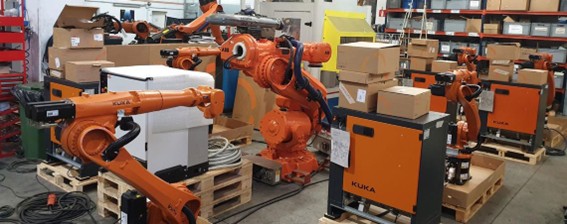
La automatización se ha transformado en un instrumento crucial para incrementar la eficacia y disminuir gastos en diferentes sectores. No obstante, es fundamental realizar las preguntas adecuadas antes de iniciar un proyecto de automatización para asegurar el éxito y optimizar el rendimiento de la inversión. Aquí exploramos tres preguntas clave que toda empresa debe considerar antes de integrar la automatización en sus procesos.
- ¿Cuáles son los objetivos y desafíos específicos que se buscan abordar con la automatización?
Previo al inicio de cualquier proyecto de automatización, es esencial tener un entendimiento preciso de los objetivos que se pretende alcanzar y los retos concretos que se pretende enfrentar. Esto puede abarcar la eficacia en las operaciones, disminuir gastos, agilizar el proceso de venta o potenciar la experiencia del cliente. Por ejemplo, una empresa de manufactura puede buscar automatizar procesos repetitivos para reducir errores humanos y aumentar la producción.
- ¿Qué procedimientos industriales son los más apropiados para la automatización?
No todos los procedimientos industriales resultan ser igual de aptos para la automatización. Es crucial reconocer y dar prioridad a los procesos que son monótonos, fundamentados en normas y que podrían ser estandarizados. Estos son los procedimientos que pueden obtener mayores beneficios de la automatización y producir un rendimiento de la inversión más acelerado. Un estudio de caso de una empresa de logística mostró que la automatización de su sistema de gestión de inventarios resultó en una reducción del 25% en los costos operativos y un aumento del 30% en la precisión del inventario.
- ¿Qué tecnologías de automatización están disponibles y cuál es la más adecuada para nuestras necesidades?
Hay una diversidad de tecnologías de automatización disponibles, que abarcan desde sistemas de administración de flujos laborales hasta instrumentos de robotización de procesos (RPA) y soluciones de IA. Es imprescindible analizar las alternativas existentes y elegir la tecnología que mejor se ajuste a las necesidades y habilidades de la entidad. Por ejemplo, una empresa de servicios financieros puede optar por implementar RPA para automatizar tareas administrativas repetitivas, liberando así a los empleados para que se concentren en actividades de mayor valor añadido.
Estudios de caso y ejemplos reales
Un ejemplo notable es la implementación de la automatización en una empresa de comercio electrónico. La empresa reportó una reducción del 30% en los tiempos de procesamiento de pedidos y una disminución significativa en los errores de selección. Otro caso de éxito se encuentra en un hospital, donde la automatización se utiliza para preparar kits médicos, mejorando la precisión y reduciendo el tiempo de preparación.
La automatización puede ofrecer numerosos beneficios, pero es esencial abordar las preguntas correctas antes de la integración para garantizar el éxito del proyecto. Al comprender claramente los objetivos y desafíos, identificar los procesos adecuados para la automatización y seleccionar la tecnología más adecuada, las empresas pueden maximizar el retorno de la inversión y mejorar significativamente su eficiencia operativa. A medida que la tecnología continúa evolucionando, es probable que veamos una adopción aún mayor de soluciones automatizadas, transformando la manera en que operan las empresas en todo el mundo.